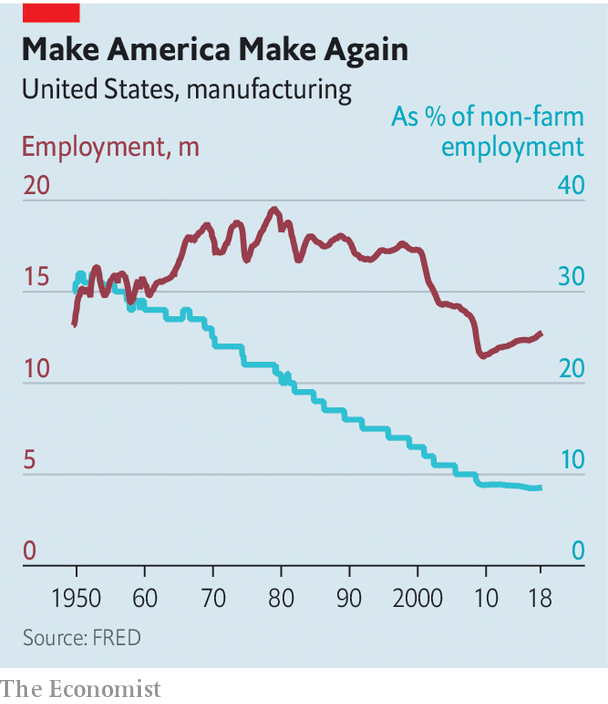
There are key elements that can help you get the best job opportunities, whether you're looking to enter the manufacturing industry or advance your career. To succeed, you will need to not only have the technical skills but also understand the market demand. Furthermore, you need to learn how communicate effectively, analyze benefits and costs, and work with others.
If you are looking for a job in research and development, you will need to be able conduct research, create new products and technologies and modify your strategies as necessary. A strong background in business development is essential.
To be an industrial engineer you must also have the ability to analyze staffing levels, assess processes and decide what support is best for the workforce. Additionally, you will need to be able analyze products from different industries and use biological methods to make materials.
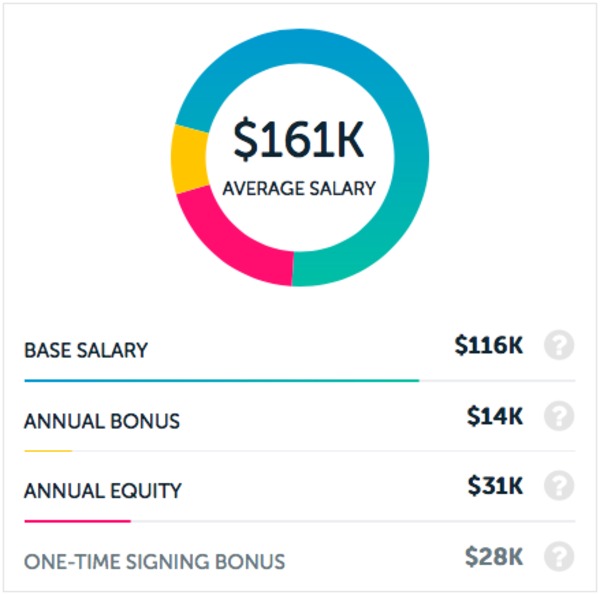
In terms of salaries, you can expect to earn around $72,234 per year as an industrial engineer. These figures include bonuses and any commissions. These aren't the only things that can impact your salary. However, they can help you get the salary you want.
If you are interested in a career of manufacturing engineer, there are many options. You can find jobs in many different industries such as aerospace, food, drink, and biotechnology. International MNCs are also available. Many companies will hire you based upon your education and professional experience.
However, it's important to remember that your salary will also depend on your work environment. Manufacturing engineers could be subject to overtime as well as profit-sharing. It's also important to be flexible in your work schedule. Finding a job that allows you to work from home can help you achieve this. This type of flexibility can be hard to apply if your job is a manual one.
According to U.S. Bureau of Labor Statistics. The demand for engineering professionals is expected to rise by 14% from now to 2030. The Bureau reports that 365,000 new manufacturing jobs will be created between now and 2021. This represents a significant improvement on the 2020 job loss.
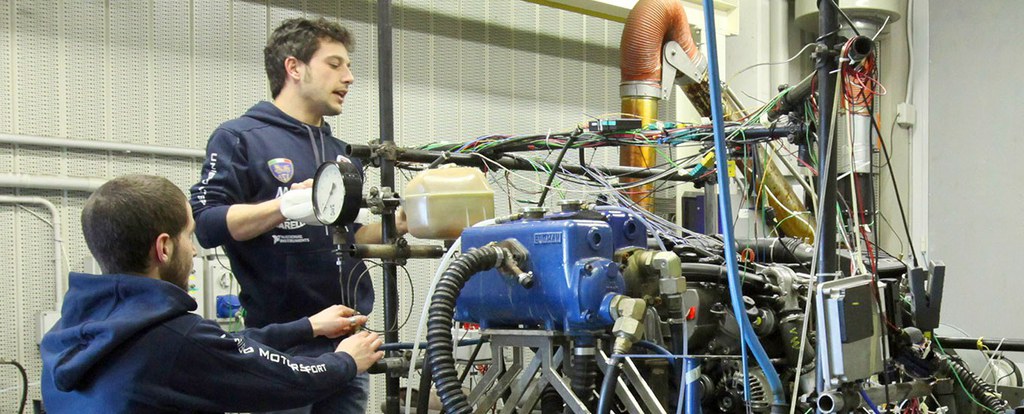
If you decide to pursue a career within the automotive industry, you will find that you could earn a very high manufacturing engineering salary. The average salary for a director working in automotive manufacturing engineering is $167.890 per annual, but there are opportunities to make more in the technology field. The technology industry is the best paying for engineers operations managers. They earn a salary that is comparable to those in manufacturing engineering.
Research and development managers make substantial amounts of money. On average, they make around $167,250 per year. They're more likely to be awarded a Master’s Degree than directors in manufacturing engineering. Despite this, they are more likely earn a Doctoral.
FAQ
What is the job of a manufacturer manager?
The manufacturing manager should ensure that every manufacturing process is efficient and effective. They should be alert for any potential problems in the company and react accordingly.
They should also know how to communicate with other departments such as sales and marketing.
They should be up to date on the latest trends and be able apply this knowledge to increase productivity and efficiency.
How can manufacturing avoid production bottlenecks
Production bottlenecks can be avoided by ensuring that processes are running smoothly during the entire production process, starting with the receipt of an order and ending when the product ships.
This includes both quality control and capacity planning.
Continuous improvement techniques such Six Sigma are the best method to accomplish this.
Six Sigma can be used to improve the quality and decrease waste in all areas of your company.
It emphasizes consistency and eliminating variance in your work.
What skills is required for a production planner?
A production planner must be organized, flexible, and able multitask to succeed. Effective communication with clients and colleagues is essential.
What does warehouse refer to?
A warehouse is a place where goods are stored until they are sold. You can have it indoors or outdoors. Sometimes, it can be both an indoor and outdoor space.
What are the 7 Rs of logistics.
The acronym 7R's of Logistic is an acronym that stands for seven fundamental principles of logistics management. It was developed and published by the International Association of Business Logisticians in 2004 as part of the "Seven Principles of Logistics Management".
The acronym is composed of the following letters.
-
Responsible - ensure that all actions taken are within legal requirements and are not harmful to others.
-
Reliable - have confidence in the ability to deliver on commitments made.
-
Reasonable - make sure you use your resources well and don't waste them.
-
Realistic – consider all aspects of operations, from cost-effectiveness to environmental impact.
-
Respectful - treat people fairly and equitably.
-
Responsive - Look for ways to save time and increase productivity.
-
Recognizable - provide customers with value-added services.
How can excess manufacturing production be reduced?
It is essential to find better ways to manage inventory to reduce overproduction. This would reduce the time spent on unproductive activities like purchasing, storing and maintaining excess stock. This will allow us to free up resources for more productive tasks.
One way to do this is to adopt a Kanban system. A Kanban board is a visual display used to track work in progress. Kanban systems allow work items to move through different states until they reach their final destination. Each state is assigned a different priority.
If work is moving from one stage to the other, then the current task can be completed and moved on to the next. However, if a task is still at the beginning stages, it will remain so until it reaches the end of the process.
This allows work to move forward and ensures that no work is missed. A Kanban board allows managers to monitor how much work is being completed at any given moment. This allows them the ability to adjust their workflow using real-time data.
Lean manufacturing, another method to control inventory levels, is also an option. Lean manufacturing works to eliminate waste throughout every stage of the production chain. Anything that does not contribute to the product's value is considered waste. Here are some examples of common types.
-
Overproduction
-
Inventory
-
Unnecessary packaging
-
Excess materials
Manufacturers can reduce their costs and improve their efficiency by using these ideas.
Statistics
- In the United States, for example, manufacturing makes up 15% of the economic output. (twi-global.com)
- You can multiply the result by 100 to get the total percent of monthly overhead. (investopedia.com)
- It's estimated that 10.8% of the U.S. GDP in 2020 was contributed to manufacturing. (investopedia.com)
- Many factories witnessed a 30% increase in output due to the shift to electric motors. (en.wikipedia.org)
- In 2021, an estimated 12.1 million Americans work in the manufacturing sector.6 (investopedia.com)
External Links
How To
Six Sigma in Manufacturing:
Six Sigma is defined by "the application SPC (statistical process control) techniques to achieve continuous improvements." Motorola's Quality Improvement Department created Six Sigma at their Tokyo plant, Japan in 1986. Six Sigma's basic concept is to improve quality and eliminate defects through standardization. Many companies have adopted this method in recent years. They believe there is no such thing a perfect product or service. The main goal of Six Sigma is to reduce variation from the mean value of production. If you take a sample and compare it with the average, you will be able to determine how much of the production process is different from the norm. If the deviation is excessive, it's likely that something needs to be fixed.
Understanding the dynamics of variability within your business is the first step in Six Sigma. Once you understand that, it is time to identify the sources of variation. It is important to identify whether the variations are random or systemic. Random variations happen when people make errors; systematic variations are caused externally. Random variations would include, for example, the failure of some widgets to fall from the assembly line. However, if you notice that every time you assemble a widget, it always falls apart at exactly the same place, then that would be a systematic problem.
Once you have identified the problem, you can design solutions. This could mean changing your approach or redesigning the entire process. You should then test the changes again after they have been implemented. If they don't work you need to rework them and come up a better plan.