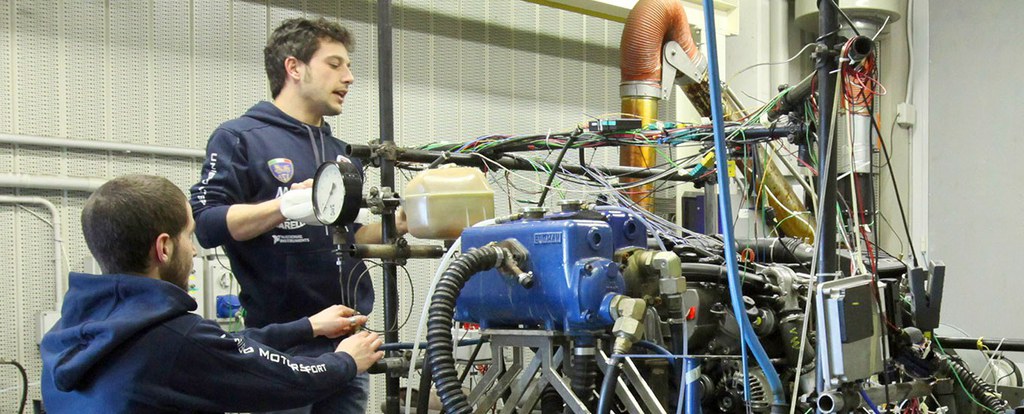
A nuclear engineer can make between six and seven figures. Aside from their regular duties, they can supervise the construction of nuclear facilities and even oversee work in closed facilities. They may have to defend their work in public. Many reasons make nuclear engineers highly desirable. Aside from their technical skills, nuclear engineers are highly valued for their leadership qualities. This profession's salary depends on many factors including education, experience, and whereabouts.
A bachelor's degree is enough to earn a salary as a nuclear engineer.
The federal government has the highest number of nuclear engineers. Other top employers include the engineering, scientific research, and development services sectors. Due to increased interest in nuclear energy, the demand for nuclear engineers in engineering and research and design will grow over the next ten years. This new technology may increase the production of commercial nuclear power plant. However, they don't currently have many.
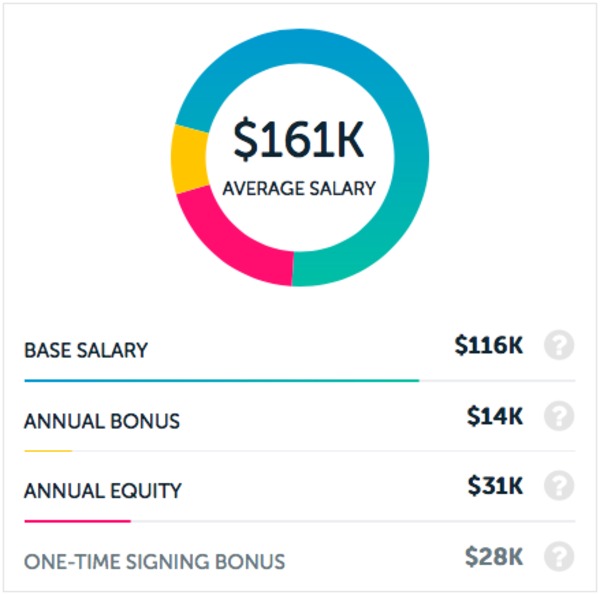
In order to become a nuclear engineer, you must have a bachelor's degree in engineering or a related field. A bachelor's in nuclear engineering could lead to an entry-level position or a better career path for those who have completed a masters degree. Some positions may require state licensure, as well. For their first few year, nuclear engineers usually work under an experienced engineer. They gain experience and take responsibility.
A master's degree in nuclear engineering is equivalent to an average salary
If you're considering a career as a nuclear engineer, you'll need to consider the salary expectations for this field. It is possible to find work at any nuclear plant. However, most people prefer to work in an office setting. The majority of people interested in a career working in nuclear energy will work in power stations and work with mechanical and electrical engineers. They will be required to integrate systems created by other professionals. Nuclear engineers are typically full-time workers and may even work more than their counterparts.
A nuclear engineer who has a Master's degree earns an average salary of $124,272 per annum, which is significantly more than the median income for all US workers. Note that salary ranges can be very different from one position to another. An average salary for nuclear engineers is $185,550. The average starting salary is $74,800, and it is among the highest in the field.
Start salary for a nuclear engineer
It is important to find out the average starting wage for nuclear engineering if you are considering a career. You will need a strong university record, and experience in the field. Although nuclear engineers might experience steady career advancement, they have the option of switching to a related field. Among other jobs, nuclear engineers are involved in manufacturing, space exploration, and medical applications of radiological materials.
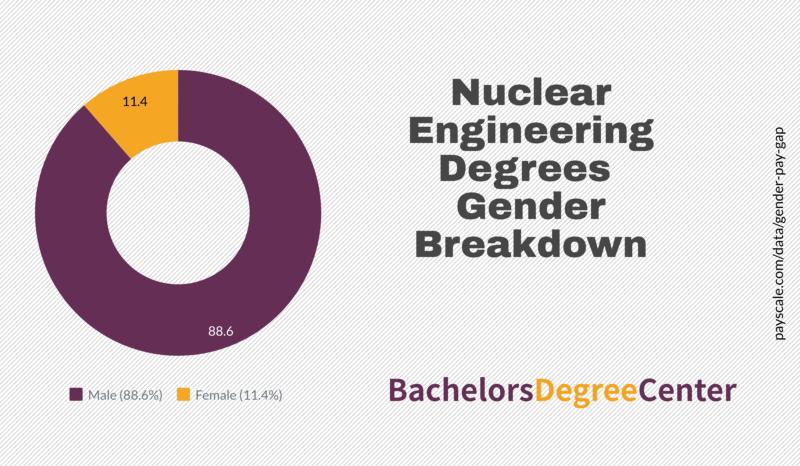
Nuclear engineers can work in many industries but the federal government is their largest employer. The operation of these facilities is overseen by Office for Nuclear Regulation. There are also other industries that employ this field, including construction and manufacturing. In the future, employment opportunities for nuclear engineers are expected to grow as the use of nuclear power increases, but the shortage of graduates will limit job prospects for those with this degree. There are currently limited jobs available for nuclear engineers by the federal government, but many companies are now hiring these professionals.
FAQ
What jobs are available in logistics?
There are many kinds of jobs available within logistics. Here are some examples:
-
Warehouse workers: They load and unload trucks, pallets, and other cargo.
-
Transportation drivers - They drive trucks and trailers to deliver goods and carry out pick-ups.
-
Freight handlers - They sort and pack freight in warehouses.
-
Inventory managers – These people oversee inventory at warehouses.
-
Sales reps are people who sell products to customers.
-
Logistics coordinators - They plan and organize logistics operations.
-
Purchasing agents - They purchase goods and services needed for company operations.
-
Customer service representatives – They answer emails and phone calls from customers.
-
Shipping clerks - They process shipping orders and issue bills.
-
Order fillers are people who fill orders based only on what was ordered.
-
Quality control inspectors - They check incoming and outgoing products for defects.
-
Others - There are many types of jobs in logistics such as transport supervisors and cargo specialists.
How can I learn about manufacturing?
The best way to learn about manufacturing is through hands-on experience. However, if that's not possible, you can always read books or watch educational videos.
What is production planning?
Production Planning involves developing a plan for all aspects of the production, including scheduling, budgeting, casting, crew, location, equipment, props, etc. This document will ensure everything is in order and ready to go when you need it. This document should include information about how to achieve the best results on-set. It should include information about shooting locations, casting lists, crew details, equipment requirements, and shooting schedules.
First, you need to plan what you want to film. You may have decided where to shoot or even specific locations you want to use. Once you've identified the locations and scenes you want to use, you can begin to plan what elements you need for each scene. One example is if you are unsure of the exact model you want but decide that you require a car. If this is the case, you might start searching online for car models and then narrow your options by selecting from different makes.
After you have selected the car you want, you can begin to think about additional features. Do you need people sitting in the front seats? You might also need someone to help you get around the back. You might want to change your interior color from black and white. These questions will help guide you in determining the ideal look and feel for your car. Also, think about what kind of shots you would like to capture. What type of shots will you choose? Maybe you want to show your engine or the steering wheel. These factors will help you determine which car style you want to film.
Once you have all the information, you are ready to create a plan. You can create a schedule that will outline when you must start and finish your shoots. The schedule will show you when to get there, what time to leave, and when to return home. Everyone will know what they need and when. Book extra staff ahead of time if you need them. You don't want to hire someone who won't show up because he didn't know.
Your schedule will also have to be adjusted to reflect the number of days required to film. Some projects only take one or two days, while others may last weeks. You should consider whether you will need more than one shot per week when creating your schedule. Multiple shots at the same location can increase costs and make it more difficult to complete. If you aren't sure whether you need multiple shots, it is best to take fewer photos than you would like.
Budget setting is an important part of production planning. You will be able to manage your resources if you have a realistic budget. Remember that you can always reduce the budget later on if you run into unforeseen problems. However, it is important not to overestimate the amount that you will spend. Underestimating the cost will result in less money after you have paid for other items.
Production planning is a complicated process. But once you understand how everything works together, it becomes much easier to plan future project.
What is the job of a manufacturer manager?
Manufacturing managers must ensure that manufacturing processes are efficient, effective, and cost-effective. They should be aware of any issues within the company and respond accordingly.
They must also be able to communicate with sales and marketing departments.
They should also be aware of the latest trends in their industry and be able to use this information to help improve productivity and efficiency.
What are the essential elements of running a logistics firm?
To run a successful logistics company, you need a lot knowledge and skills. You must have good communication skills to interact effectively with your clients and suppliers. You must be able analyze data and draw out conclusions. You must be able to work well under pressure and handle stressful situations. You need to be innovative and creative to come up with new ways to increase efficiency. You need to have strong leadership qualities to motivate team members and direct them towards achieving organizational goals.
To meet tight deadlines, you must also be efficient and organized.
How can efficiency in manufacturing be improved?
The first step is to identify the most important factors affecting production time. Next, we must find ways to improve those factors. If you aren't sure where to begin, think about the factors that have the greatest impact on production time. Once you have identified the factors, then try to find solutions.
What skills do production planners need?
You must be flexible and organized to become a productive production planner. Also, you must be able and willing to communicate with clients and coworkers.
Statistics
- According to the United Nations Industrial Development Organization (UNIDO), China is the top manufacturer worldwide by 2019 output, producing 28.7% of the total global manufacturing output, followed by the United States, Japan, Germany, and India.[52][53] (en.wikipedia.org)
- According to a Statista study, U.S. businesses spent $1.63 trillion on logistics in 2019, moving goods from origin to end user through various supply chain network segments. (netsuite.com)
- Many factories witnessed a 30% increase in output due to the shift to electric motors. (en.wikipedia.org)
- [54][55] These are the top 50 countries by the total value of manufacturing output in US dollars for its noted year according to World Bank.[56] (en.wikipedia.org)
- Job #1 is delivering the ordered product according to specifications: color, size, brand, and quantity. (netsuite.com)
External Links
How To
How to Use 5S for Increasing Productivity in Manufacturing
5S stands for "Sort", "Set In Order", "Standardize", "Separate" and "Store". The 5S methodology was developed at Toyota Motor Corporation in 1954. It allows companies to improve their work environment, thereby achieving greater efficiency.
This method has the basic goal of standardizing production processes to make them repeatable. This means that daily tasks such as cleaning and sorting, storage, packing, labeling, and packaging are possible. Workers can be more productive by knowing what to expect.
Implementing 5S involves five steps: Sort, Set in Order, Standardize Separate, Store, and Each step requires a different action, which increases efficiency. You can make it easy for people to find things later by sorting them. Once you have placed items in an ordered fashion, you will put them together. Once you have separated your inventory into groups and organized them, you will store these groups in easily accessible containers. Make sure everything is correctly labeled when you label your containers.
This requires employees to critically evaluate how they work. Employees need to be able understand their motivations and discover alternative ways to do them. To implement the 5S system, employees must acquire new skills and techniques.
In addition to increasing efficiency, the 5S method also improves morale and teamwork among employees. Once they start to notice improvements, they are motivated to keep working towards their goal of increasing efficiency.