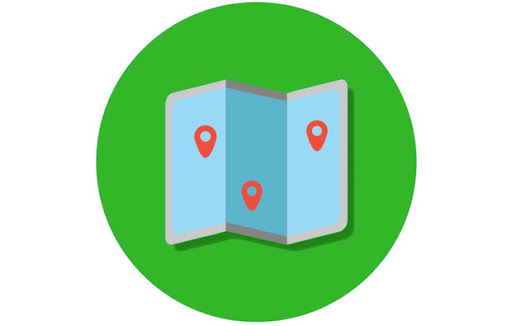
The foundation for continuous improvement is PDCA (Plan, Do, Check, Act). If implemented properly, this method of improvement can yield significant results. Employee involvement is crucial to continuous improvement. A variety of resources are needed to implement the process. While measuring and costing are essential to the process, they are not its only benefit. Without employees and customers, the PDCA cycle will not be complete.
PDCA cycle
Continuous improvement requires that you apply the PDCA cycle to every aspect of your business. This cycle works by continuously improving a process and building on past improvements. You may be able to see new trends in the data as the team tests a new process or you may uncover a new baseline, both of which reveal new areas for improvement. The PDCA Cycle is a great tool for identifying improvements opportunities. However, you must use it carefully and in a controlled way.
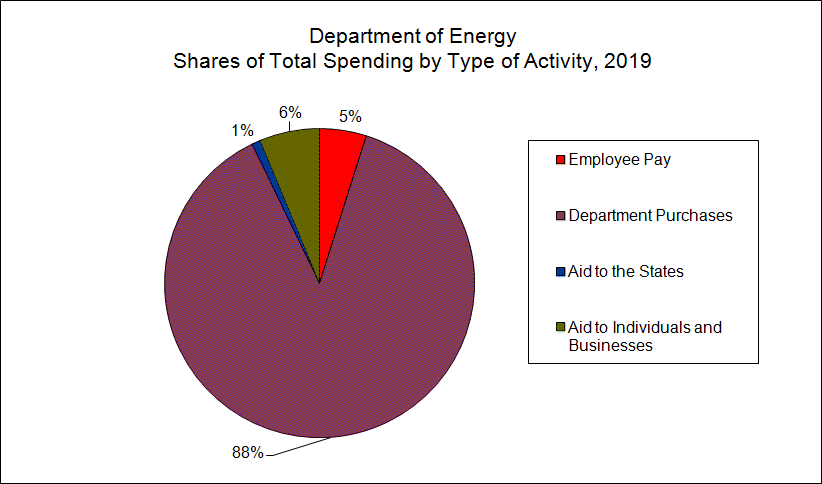
Employee involvement
While employee involvement can be called many different things, all effective organizations recognize its importance. Research has shown that employee involvement is closely linked to key work outcomes. There are several types of employee involvement: direct communication, representative participation through unions and upward problem solving. These types of employee involvement are often strengthened by the culture, leadership, and environment of an organization. These are just a few examples of employee involvement that have been successful.
Measurement
Many companies have begun to incorporate measurements in their continuous improvement plans. The Deming cycle, which was introduced by W. Edwards Deming, includes a Check phase that evaluates the progress of an improvement initiative against its objectives. If the results fall below expectations, adjustments are made to improve them. Unless the results are satisfactory, the cycle will be repeated. In the case of continuous improvement, these processes are a part of the process itself.
Costs
For CI to be considered cost-effective, it is essential that an enterprise-wide cost evaluation of CI efforts be done. The cost-benefit analysis should be based on the business imperative of achieving the highest possible customer satisfaction and employee engagement scores. The cost-benefit analysis should also include the ROI of the CI initiatives and the fine-tuning of budgets to ensure success. The cost-benefit analysis should focus on improving the performance of key business processes and key performance areas by benchmarking them with leading competitors and industry averages.
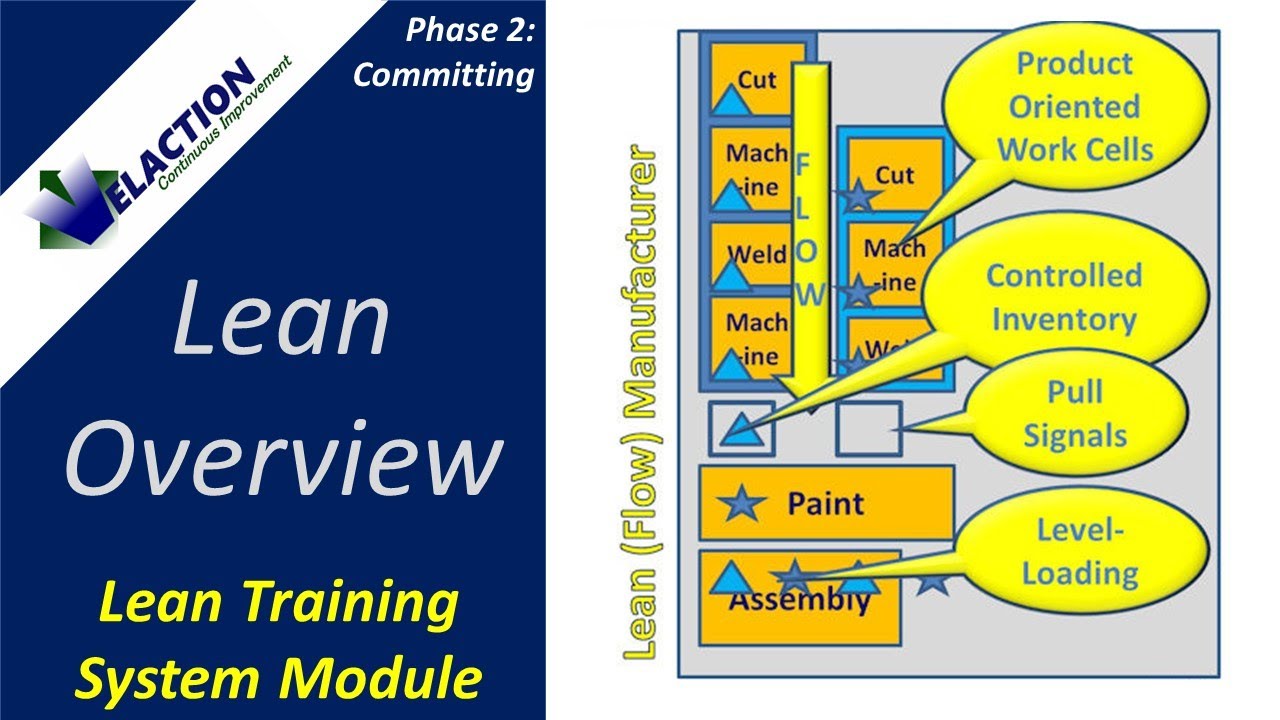
Benefits
Continuous improvement brings clear benefits. Focusing on learning and failure will lead to more breakthroughs. Encourage employees to find ways to improve their work and give them ownership. A team that invests in the testing of new technologies or tools can also result in empowered employees. The benefits of continuous improvement extend beyond the savings in money. Employee satisfaction is improved and work can be made easier by making positive changes.
FAQ
What does warehouse refer to?
Warehouses and storage facilities are where goods are kept before being sold. It can be indoors or out. It may also be an indoor space or an outdoor area.
What jobs are available in logistics?
There are many jobs available in logistics. Here are some:
-
Warehouse workers: They load and unload trucks, pallets, and other cargo.
-
Transportation drivers – They drive trucks or trailers to transport goods and perform pick-ups.
-
Freight handlers, - They sort out and pack freight in warehouses.
-
Inventory managers – These people oversee inventory at warehouses.
-
Sales reps - They sell products and services to customers.
-
Logistics coordinators – They plan and coordinate logistics operations.
-
Purchasing agents – They buy goods or services necessary to run a company.
-
Customer service representatives - Answer calls and email from customers.
-
Shipping clerks: They process shipping requests and issue bills.
-
Order fillers are people who fill orders based only on what was ordered.
-
Quality control inspectors: They inspect outgoing and incoming products for any defects.
-
Others - There are many types of jobs in logistics such as transport supervisors and cargo specialists.
Is it necessary to be familiar with Manufacturing Processes before we learn about Logistics.
No. No. Knowing about manufacturing processes will help you understand how logistics works.
What can I do to learn more about manufacturing?
Hands-on experience is the best way to learn more about manufacturing. But if that is not possible you can always read books and watch educational videos.
Why automate your warehouse?
Modern warehouses have become more dependent on automation. E-commerce has brought increased demand for more efficient and quicker delivery times.
Warehouses have to be flexible to meet changing requirements. To do so, they must invest heavily in technology. Automation of warehouses offers many benefits. Here are some benefits of investing in automation
-
Increases throughput/productivity
-
Reduces errors
-
Increases accuracy
-
Boosts safety
-
Eliminates bottlenecks
-
Allows companies scale more easily
-
Increases efficiency of workers
-
The warehouse can be viewed from all angles.
-
Enhances customer experience
-
Improves employee satisfaction
-
Reduces downtime and improves uptime
-
Quality products delivered on time
-
Removes human error
-
Helps ensure compliance with regulations
What does it take for a logistics enterprise to succeed?
You need to have a lot of knowledge and skills to manage a successful logistic business. To communicate effectively with clients and suppliers, you must be able to communicate well. It is important to be able to analyse data and draw conclusions. You need to be able work under pressure and manage stressful situations. In order to innovate and create new ways to improve efficiency, creativity is essential. You will need strong leadership skills to motivate and direct your team members towards achieving their organizational goals.
It is also important to be efficient and well organized in order meet deadlines.
How can excess manufacturing production be reduced?
It is essential to find better ways to manage inventory to reduce overproduction. This would reduce the time needed to manage inventory. We could use these resources to do other productive tasks.
This can be done by using a Kanban system. A Kanban Board is a visual display that tracks work progress. Kanban systems are where work items travel through a series of states until reaching their final destination. Each state is assigned a different priority.
If work is moving from one stage to the other, then the current task can be completed and moved on to the next. If a task is still in its beginning stages, it will continue to be so until it reaches the end.
This allows for work to continue moving forward, while also ensuring that there is no work left behind. Managers can see how much work has been done and the status of each task at any time with a Kanban Board. This allows them to adjust their workflows based on real-time information.
Lean manufacturing is another way to manage inventory levels. Lean manufacturing is about eliminating waste from all stages of the production process. Waste includes anything that does not add value to the product. These are some of the most common types.
-
Overproduction
-
Inventory
-
Packaging not required
-
Exceed materials
By implementing these ideas, manufacturers can improve efficiency and cut costs.
Statistics
- You can multiply the result by 100 to get the total percent of monthly overhead. (investopedia.com)
- [54][55] These are the top 50 countries by the total value of manufacturing output in US dollars for its noted year according to World Bank.[56] (en.wikipedia.org)
- Job #1 is delivering the ordered product according to specifications: color, size, brand, and quantity. (netsuite.com)
- In the United States, for example, manufacturing makes up 15% of the economic output. (twi-global.com)
- In 2021, an estimated 12.1 million Americans work in the manufacturing sector.6 (investopedia.com)
External Links
How To
How to use the Just In-Time Production Method
Just-in-time is a way to cut costs and increase efficiency in business processes. This is where you have the right resources at the right time. This means that you only pay the amount you actually use. Frederick Taylor first coined this term while working in the early 1900s as a foreman. Taylor observed that overtime was paid to workers if they were late in working. He decided to ensure workers have enough time to do their jobs before starting work to improve productivity.
JIT is a way to plan ahead and make sure you don't waste any money. You should also look at the entire project from start to finish and make sure that you have sufficient resources available to deal with any problems that arise during the course of your project. You can anticipate problems and have enough equipment and people available to fix them. This will prevent you from spending extra money on unnecessary things.
There are many JIT methods.
-
Demand-driven: This is a type of JIT where you order the parts/materials needed for your project regularly. This will let you track the amount of material left over after you've used it. This will allow you to calculate how long it will take to make more.
-
Inventory-based: This allows you to store the materials necessary for your projects in advance. This allows one to predict how much they will sell.
-
Project-driven: This is an approach where you set aside enough funds to cover the cost of your project. You will be able to purchase the right amount of materials if you know what you need.
-
Resource-based: This is the most common form of JIT. Here you can allocate certain resources based purely on demand. If you have many orders, you will assign more people to manage them. If you don't receive many orders, then you'll assign fewer employees to handle the load.
-
Cost-based: This is the same as resource-based except that you don't care how many people there are but how much each one of them costs.
-
Price-based: This is similar to cost-based but instead of looking at individual workers' salaries, you look at the total company price.
-
Material-based: This is very similar to cost-based but instead of looking at total costs of the company you are concerned with how many raw materials you use on an average.
-
Time-based JIT: A variation on resource-based JIT. Instead of worrying about how much each worker costs, you can focus on how long the project takes.
-
Quality-based JIT - This is another form of resource-based JIT. Instead of worrying about the costs of each employee or how long it takes for something to be made, you should think about how quality your product is.
-
Value-based JIT: One of the most recent forms of JIT. You don't worry about whether the products work or if they meet customer expectations. Instead, you are focused on adding value to the marketplace.
-
Stock-based. This method is inventory-based and focuses only on the actual production at any given point. It's used when you want to maximize production while minimizing inventory.
-
Just-in time (JIT), planning: This is a combination JIT/supply chain management. It refers to the process of scheduling the delivery of components as soon as they are ordered. It is essential because it reduces lead-times and increases throughput.