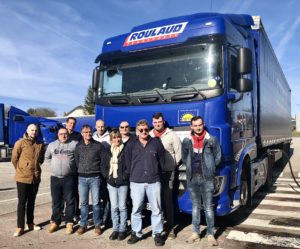
Lean services applies lean manufacturing principles to the service sector. HMRC in the UK, and health care providers in the USA have both adopted this approach to their production. Lean services are designed to reduce waste, improve customer satisfaction, and decrease costs. Lean services are available to all businesses, regardless of whether they're small startups or global giants.
Lean manufacturing
Lean manufacturing focuses on eliminating waste. This process can help businesses improve their overall productivity and reduce operating costs. It also increases employee satisfaction. It can help increase profits. It can improve the lead time of a product and increase profits. Additionally, lean manufacturing can help companies improve their customer base to increase their revenue streams.
Lean manufacturing takes a team approach, and a lot of talent. It is crucial that everyone in the team has a basic understanding of the process and how it works. Additionally, they must be able adapt the practices to suit the company's needs. Lean manufacturing, for example, starts with simplifying manufacturing processes. Complex manufacturing processes are difficult to spot waste and inefficiencies. This simplifies the process and creates a culture of continuous improvement. This will allow your employees the freedom to search for inefficiencies.
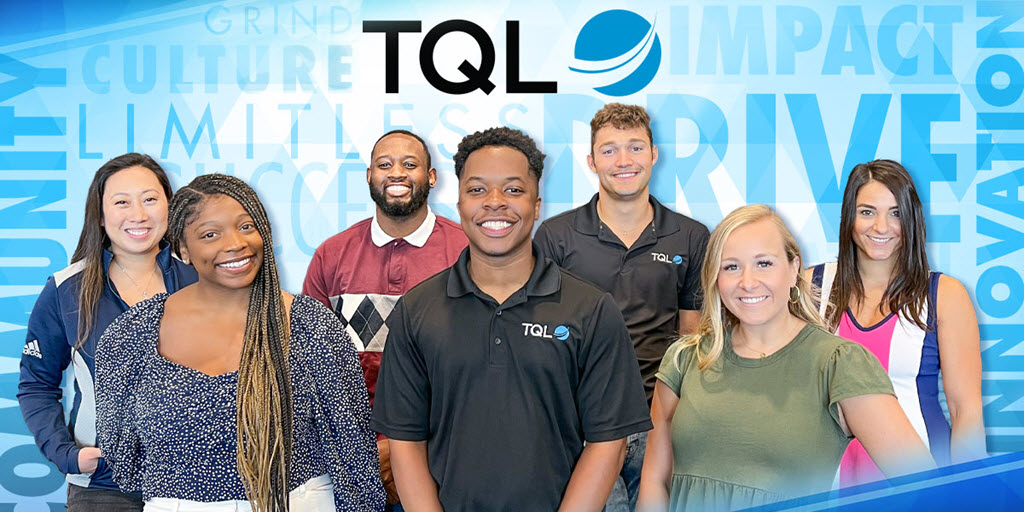
Companies can improve their efficiency and reduce their lead times by using lean manufacturing services. MXGlobal, which offers lean implementation, is one such company. It has successfully consulted Japanese corporations with U.S. presence. Lean manufacturing services offered by the firm are designed to help businesses expand internationally and reach their business goals.
Lean manufacturing services help businesses create an environment that will maximize profits. They work to reduce waste and increase productivity. There are eight types. They include excess production, inventory, and transport. These wastes can increase costs and decrease customer satisfaction.
Lean operations management
In order to implement lean operation management for lean service, organizations need to first understand what they are trying accomplish. As the name implies, it is a systematic approach that seeks to create value for the end customers. Value is what drives sales and what consumers want from a product/service. Start by mapping the various steps involved in the creation of a product/service and asking, "What adds to the customer?"
Continuous improvement is the goal of lean management systems. Continuous improvement is the core of this approach. It will ensure that your team is able to deliver work assignments on time and with minimal effort. In addition, this method reduces waste from production processes, and optimizes overhead and storage costs. The four principles of lean management include continuous improvement, minimizing waste, reducing cycle time, and ensuring continuous workflows.
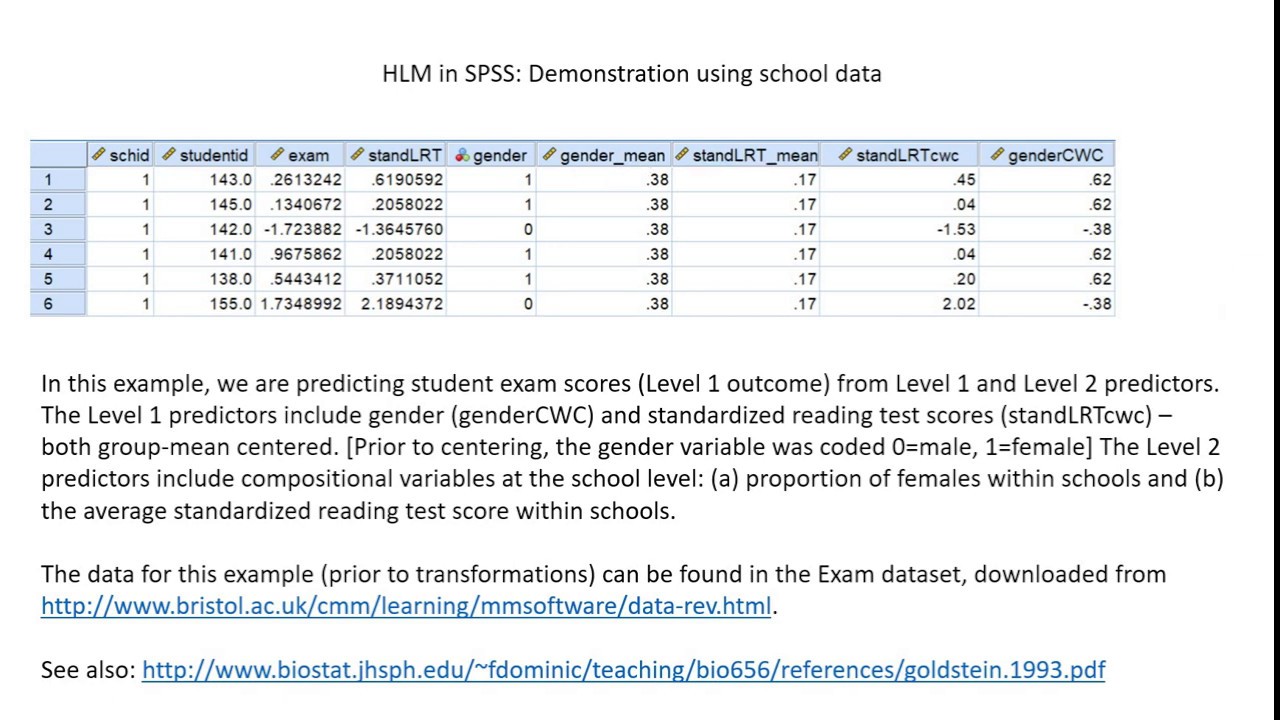
Lean operations management - lean services, focuses on creating greater value for customers by using fewer resources. While it can be hard to find intangible and non-tangible wastes within a service environment. Lean principles seek to eliminate these. By eliminating waste, companies can create value for their customers and maximize profits.
FAQ
How can excess manufacturing production be reduced?
In order to reduce excess production, you need to develop better inventory management methods. This would reduce the time needed to manage inventory. By doing this, we could free up resources for other productive tasks.
You can do this by adopting a Kanban method. A Kanban board can be used to monitor work progress. Kanban systems allow work items to move through different states until they reach their final destination. Each state represents a different priority.
As an example, if work is progressing from one stage of the process to another, then the current task is complete and can be transferred to the next. A task that is still in the initial stages of a process will be considered complete until it moves on to the next stage.
This allows you to keep work moving along while making sure that no work gets neglected. Managers can see how much work has been done and the status of each task at any time with a Kanban Board. This data allows them adjust their workflow based upon real-time data.
Lean manufacturing is another way to manage inventory levels. Lean manufacturing works to eliminate waste throughout every stage of the production chain. Waste includes anything that does not add value to the product. There are several types of waste that you might encounter:
-
Overproduction
-
Inventory
-
Packaging not required
-
Material surplus
These ideas will help manufacturers increase efficiency and lower costs.
What types of jobs can you find in logistics
There are many types of jobs in logistics. Here are some:
-
Warehouse workers - They load trucks and pallets.
-
Transportation drivers - They drive trucks and trailers to deliver goods and carry out pick-ups.
-
Freight handlers: They sort and package freight in warehouses.
-
Inventory managers - These are responsible for overseeing the stock of goods in warehouses.
-
Sales reps - They sell products and services to customers.
-
Logistics coordinators - They plan and organize logistics operations.
-
Purchasing agents are those who purchase goods and services for the company.
-
Customer service representatives are available to answer customer calls and emails.
-
Shippers clerks - They process shipping order and issue bills.
-
Order fillers: They fill orders based off what has been ordered and shipped.
-
Quality control inspectors: They inspect outgoing and incoming products for any defects.
-
Others - There are many other types of jobs available in logistics, such as transportation supervisors, cargo specialists, etc.
Is automation important in manufacturing?
Automation is important not only for manufacturers but also for service providers. Automation allows them to deliver services quicker and more efficiently. In addition, it helps them reduce costs by reducing human errors and improving productivity.
What is the difference between Production Planning, Scheduling and Production Planning?
Production Planning (PP) refers to the process of determining how much production is needed at any given moment. This is accomplished by forecasting the demand and identifying production resources.
Scheduling refers the process by which tasks are assigned dates so that they can all be completed within the given timeframe.
Statistics
- According to the United Nations Industrial Development Organization (UNIDO), China is the top manufacturer worldwide by 2019 output, producing 28.7% of the total global manufacturing output, followed by the United States, Japan, Germany, and India.[52][53] (en.wikipedia.org)
- Job #1 is delivering the ordered product according to specifications: color, size, brand, and quantity. (netsuite.com)
- It's estimated that 10.8% of the U.S. GDP in 2020 was contributed to manufacturing. (investopedia.com)
- Many factories witnessed a 30% increase in output due to the shift to electric motors. (en.wikipedia.org)
- You can multiply the result by 100 to get the total percent of monthly overhead. (investopedia.com)
External Links
How To
How to Use 5S for Increasing Productivity in Manufacturing
5S stands in for "Sort", the "Set In Order", "Standardize", or "Separate". Toyota Motor Corporation was the first to develop the 5S approach in 1954. This methodology helps companies improve their work environment to increase efficiency.
This method aims to standardize production processes so that they are repeatable, measurable and predictable. Cleaning, sorting and packing are all done daily. This knowledge allows workers to be more efficient in their work because they are aware of what to expect.
Five steps are required to implement 5S: Sort, Set In Order, Standardize. Separate. Each step involves a different action which leads to increased efficiency. By sorting, for example, you make it easy to find the items later. Once you have placed items in an ordered fashion, you will put them together. You then organize your inventory in groups. Labeling your containers will ensure that everything is correctly labeled.
Employees must be able to critically examine their work practices. Employees must be able to see why they do what they do and find a way to achieve them without having to rely on their old methods. In order to use the 5S system effectively, they must be able to learn new skills.
In addition to improving efficiency, the 5S system also increases morale and teamwork among employees. They are more motivated to achieve higher efficiency levels as they start to see improvement.